More eco-friendly scarves
The environmental benefits of digital printing
With inkjet methods, usual forms of vast waste are no longer created: the only waste remaining is linked to the maintenance of the print heads.
This method has been entering the textile process market progressively over the past few years, but technical limitations have prevented a widespread market adoption. Speeds were limited to maximal 5 m/min due to required intermitting operation being used in most existing digital textile printers. This pales in comparison to traditional finishing process speeds reaching up to 40 m/min.
The environmental benefits — which include reduced energy and water consumption, but also less pollution — arise from the fact that we are able to reproduce technical textiles with the same printing quality that we can see with current technologies, but we achieve this by using less than 10% of the chemicals used normally*.

Conventional processes
On the other hand, conventional processes — known as rotary screen printing — have required for years a high amount of chemicals to be applied on the textile, involving excessive amounts of water and energy. The process involves a different screen for each colour required in the final design, and a certain amount of print paste needs to be produced to ensure quality throughout the whole lot. This paste remains in the screens, eventually becomes waste and has to be cleaned using water, which then needs to be treated.
In total, it is estimated that 90 % of chemicals used in dyeing operations do not stay on the fibre and eventually leak into the environment*.
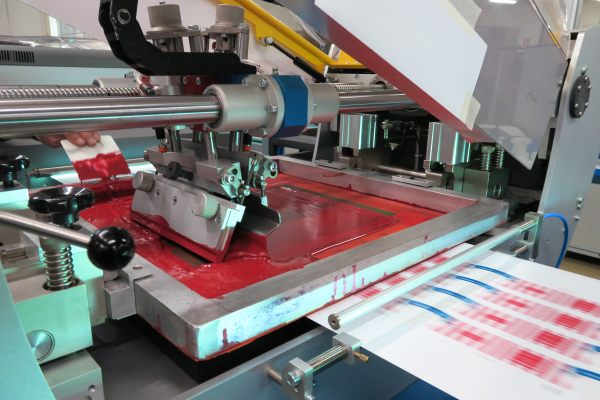
(*Source: https://cordis.europa.eu /article/rcn/118620/en, interview with Gerrit Koele, project coordinator and managing director of TenCate Digital Finishing from research*eu results magazine, n° 48 pages 12-13).